If you have been troubled by a lots of problems and errors during injection molding and looking for fast ways to troubleshoot them, then do not worry, you are at the right place. We will discuss about a lot of common errors that occur in injection molding cycle.
1.) Air bubbles in Injection Molded part/Blisters on part surface

A blister is a raised area on the plastic surface, very similar to the medical condition of the same name. Many people have no clue as to what's the reason of air bubble in injection molded part.It is generally the product of too much heat on the tool or by inadequate cooling or venting. Depending on the type of tool, you can also find areas where full coverage is not working. For instance, if the injector has a flow pattern issue, it might not inject all the resin at once, allowing air bubbles to enter the molten resin. A hot runner tool might also suck air into the die because of area constriction, slowing the passage of the resin.
Good Solution to blisters:
Reduce the local spots with high temperatures by proper cooling in the mold
2.) Burn Marks on the molded part and its surface
Burn marks are generally caused by problems similar to blistering. They

Solution to burn marks on molded parts:
1. Improve air venting to relieve trapped air and gases.
2. Reduce the material residual time in barrel.
3. Reduce the local high temperature spots in mold by proper cooling.
3.) Burrs and Flash appearing on mold's parting line
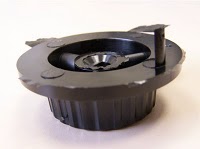
A common problem in many types of machining, burrs or flash appear on injected plastic products when extra pieces or scraps are attached to the finished piece. Burrs are usually a result of dull or inaccurately cut dies or molds. Sharpening or cleaning the dies are typically the most effective ways to remedy the situation. Mold opening during injection phase due to excessive pressure is one more resaon.
Solutions to Burrs and Flash problems:
1. Reduce the injection pressure.
2. Set clamping force to 100%.
3. Clean the parting line and check for damage or distortion on parting surface.

4.) Embedded contaminates
Then there is detritus in the finished product, it means that contaminates have somehow worked their way into the resin. A full cleaning of the machine may be necessary to find the source.
5.) Flow marks on injection molding part
Flow marks are look like discolored lines or patterns on the finished product.
When they occur, your injector might be functioning at too low a temperature.

Remedy to Flow marks on plastic parts surface:
1. Increase and decrease injection speed to get optimized speed.
2. Increase gate size.
3. Reduce the mold temperature.
6.) Lamination or flaky layer on molding walls
This occurs when contaminates are introduced into the mold or resin but manifest as shiny flake layers in the wall of the part. These are a sign that purging compound was accidentally left in the mold.
Way to remove shiny surface or flakes from manufactured part's surface:
1. Clear the barrel and refill material.

7.) Sink marks opposite to thick walls or bosses
Sink marks are small holes or depressions, similar to tiny potholes, in the surface of the piece. There are a number of reasons they might appear. First, the material might simply be insufficient for the job. A cause that is easier to remedy is temperature variation, such as too short cooling time or too high melt and mold temperatures. The mold design can contribute to these causes, so it might be necessary to start from scratch.
How to remove sink marks from part's surface:
1. Try to increase holding pressure and injection pressure.
2. Increase material temperature.
3. Decrease mold temperature.
4. Increase injection speed.
5. If none of above works, then you need to cut plastic reduce the local section thickness.

8.) Short mold or short shot on thin sections such as ribs, incomplete filling
A “short mold” refers to a mold that is not completely filled, leading to deformation or “shortened,” parts. This occurs when the resin cannot fill the mold due to blockage, bottlenecking or injection that is either too fast or too slow.
How to remove short shot and fill part completely:
1. Make arrnagement for proper air venting in mold. Add vent pins with sufficient air vent allowance on diamter, just enough to let air pass through, but not the molten plastic. This is the most accurate and suggested solution.
2. Reduce the injection speed and increase the pressure gradually. If no change is noticed till extreme parameters are reached, then refer to 1.
The above information on injection molding defects and troubleshooting is always updating and you can check back for more details later. In case you have a problem related to defects of plastic molded parts that you want solution to, except for the points mentioned above, then send me a comment below. I will definitely help you solve it ASAP. Hope you have learned something from the above Injection Molding Troubleshooting tutorial and will visit back for more information on http://plasticinjectionmouldingdesign.blogspot.com/ .
40 comments:
Great post
Even I had same problem with plastics, I will definitely try this one
Hope to see more posting related to Injection Mold
cheers
China Plastic Molding : Excellent post. I was checking continuously this blog and I am impressed! Extremely helpful information.I am extremely impressed with your writing skills.
Great post thanks.
Injection molding
Its really true my friend. Please updating your blog. Cheers..
Scottsdale Landscape Services
Hi, it is a great piece of information, i really like it. SINO Holdings Group own 5 different Mould Companies in China and well known as a best China Mold Company for its Automotive Mold, Pipe Fitting Molds, Home Appliance Mould, Packaging Mould, BMC Mould & Extrusion Dies.
Hi dear,
Great blog, The content about "Injection Molding Troubleshooting for common design defects" is really very informative. Injection molding is the most commonly used manufacturing process for the fabrication of plastic parts. A wide variety of products are manufactured using injection molding, which vary greatly in their size, complexity, and application.
Thanks,
injection moulding machine
Hey your blog is really awesome and informative too... During injection molding mostly we really face various problems... Thanks for the troubleshooting suggestions...
Plastic Moulding
Great information. Its really very useful. Thanks for the content posted.
Injection Mold Service China
Great Post !!! And the way you have described about injection molding troubleshooting and solution is really excellent very easy to understand. I like it... Thanks and Keep up Posting.
Mold Makers in China
I have seen the blog and read the above content that you have described about China molding .You have given few points that is really helpful and important for all. Thanks for sharing!
I gone through Your post it is really good. Useful content. Nice to read. i have blog for Plastic Injection moulders in India
see my products also
Plastic Injection moulders in India
This short article posted only at the web site is truly good.plastic pellets
Hi Dear, have you been certainly visiting this site daily, if that's the case you then will certainly get good knowledge.Password Manager - LogmeOnce
It's not my very first time to visit this blog; I’m visiting this daily and acquire superb info from here day by day.my lifestyle
Thankfulness to my dad who informed me relating to this blog, this website is really amazing.easy payday loans
Many thanks for the exciting blog posting! I actually added your blog to my favorites and will look forward for more updates. Great Job, Keep it up..
custom plastic injection molding
It is very a great post. I’d hope that you will continue to bring us more great things like this.
Bluestar Mould
thanks, I know your blog very well, I love your blog and I hope you continue to make such a blog.
mold manufacturer china
injection mold china
thanks, I know your blog very well, I love your blog and I hope you continue to make such a blog.
Thank you.. All the information in this post is correct and good. I love your blog.
injection mold china
injection mold company china
Interesting Article. Hoping that you will continue posting an article having a useful information. Plastic Injection Molding
We provide the best injection molding at a very affordable price we have years of experience in this field we are the leading manufacturing company of injection mould.
For More Information Visit Here -- plastic mold
injection molded parts
Looking for A plastic injection mold China company? We offer the best quality plastic mold, injection mold, your best, plastic injection molding China supplier.
A very interesting read and a great post. thanks for sharing this information.
Plastic Mold Company
We are leading China Mold Company and custom plastic Molding parts Company. We are a manufacturer of plastic injection mold making, molding plastics, china mold factory, and plastic mold in china. Contact us - +86 0769 3334-0577 - For More Information Visit Here -- Mould making companies
Thanks for sharing this blog, this blog is very helpful information for every one.
china mold factory
china mold maker
The answer from playing a joker end credit gambling game should not be too stressful, because what happened may not mean that we should http://pameboughs.jigsy.com/#builder always be successful, but we should learn to deal with what is happening. Success is what happened.
Online casinos online, we newtown casino agent have to ask ourselves what we decide to play, but this still allows us to see what each type means, whihttps://ingerpyan.doodlekit.com/home ch may be difficult for us to find answers on how to look at our decisions despite the stories that are happening Both are reasonable from different perspectives.
This blog is really impressive.Thanks for sharing such an importance piece of information. This Injection Molding Troubleshooting is helpful for High Volume Injection Molding process.
Then stop immediately because good ntc33 pc download slot machine games must stop immediately when the button is pressed, otherwise, The chance of losing income or winning a big prize is slim. Considered to have been observed before choosing to play a real game. https://penzu.com/p/d5a145b6
I always enjoy your posts, but this was one of the best. Great writing and plenty of sound knowledge shared.
Safety Nets Manufacturer
this has greatly affected the standard of these that have adamantly refused to embrace it.
China Custom Plastic Injection Molding Maker
There is a great herbal man called Dr voodoo who can cure Hepatitis B virus and other deadly diseases with the use of natural herbs to cure Hepatitis B virus problems. He is from Africa and he is a great doctor and he can also cure you as well if you are have the problem And other deadly disease and here is email address voodoospelltemple66@gmail.com or Whatsapp +2348140120719 HERPES CURE,CANCER CURE,HIV/AIDS CURE,HPV CURE
I'm 61 years old. I contracted HPV in 2011' I has be taking lot treatment for it and embarrassed some months ago the wart stated coming out seriously, I used lot recommendation because there was lot warts around my anus and was so . but today I'm totally happy I got the virus eliminated by using natural treatment from Dr voodoo herbal center after his treatment I got cured. all the warts went away' seriously believed Dr. voodoo he have the cure for human papillomavirus because he has eliminated hpv been in my body since 2011, Dr. voodoo make it possible for me. Here is Dr. voodoo email: voodoospelltemple66@gmail.com or WhatsApp him via +2348140120719 he is welled capable of curing terrible diseases.
This is an excellent article. The Injection Molding Manufacturer technology that has been made in this discipline has always astounded me. The precise intricacies and engineering are excellent, and it's amazing how they manage to make such a high-quality injection molded product with little or no assembly! The procedure for thermoset injection molding is also pretty similar to that of thermoplastic injection molding.
Thanks for sharing the best information about this blog, it gives the useful details! Please keep sharing such post.
Injection Mold Design China
Best Injection Molding Company Highly recommend Best Injection Molding Company for top-notch quality, efficient service, and reliable production. Exceptional team and results.
Post a Comment