The technical data sheet of Grilamid, both TR90 and TR 55 provides us with essential properties that Grilamid possesses, and renders it as the best choice of transparent material. I have often seen a lot of clear plastic parts cracking and bending too much, but Grilamid has got rid of this problem in transparent plastic processing.
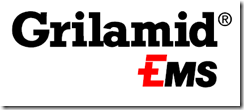
Now I will provide you with a few basic runner and gating
design guidelines for Grilamid injection molding processing that should be incorporated into tooling and molds. Although this information is available freely on the Grilamid website, I though it would be good to share it here to save time of those reading this article. To achieve an optimal mold-fill and to avoid sink marks, a central gate at the thickest section of the moulding is recommended. Pin point gate (direct) or tunnel gates are more economical and more common with technical molding.
To avoid premature solidification of the melt and difficult mould filing, the following points should be considered:
Gate Diameter: 0.8 x thickest wall section of the injection molding part
Runner Diameter: 1.4 x thickest wall section of the injection molding part (but minimum 4 mm)
The drying time for Grilamid is a bit long, which is understandably so, as most of the clear resins require a long drying time to avoid bubbles and air traps due to moisture. It needs a Desiccant dryer and the drying time needs to be over 5 hours with a temperature of 80 degrees Celsius. If you use a vacuum oven, you need to dry it for at least 8 hours at the same temperature.
Will continue with this post later when we actually mold the Grilamid part to update with the optimum injection and processing conditions on our plastic processing equipment. Make sure that you bookmark the site to get updated information on Plastic Injection Mold Design for various polymers.
4 comments:
Hi there,
Have you had any problems with plasticising time varying/ feeding problems during plasticising with Grilamid TR55? I am working on a medical overmoulding product where the plasticiding time and shot size varies a lot. Its a calibrated machine with a clean, new screw and barrel. 20mm general purpose screw with a 60 second cycle time. Any ideas would be great thanks! The material has been dried to 0.02%.
This blog is really impressive. Contact Best Plastic Manufacturing in USA to get best services.
Keep it up, This gives me very useful information. Thanks for sharing this with us. Best Plastic Injection Molding Company
Loan Opportunity Offered By Mr, Benjamin That Save My Family From Financial Bondage {lfdsloans@lemeridianfds.com / lfdsloans@outlook.com}
Hello Everyone, I am Putri Adiratnaa single mom from Jakarta, I would like to share this great testimony on how I got a loan from Mr, Benjamin, when we were driven out of our home when I couldn't pay my bills anymore, After being scammed by various companies online and denied a loan from my bank and some other credit union I visited. My children were taken by the foster care, I was all alone in the street. The day i shamefully walked into an old school mate who introduced me to Daisy Maureen. At first I told her that I am not ready to take any risk of requesting a loan online anymore, but she assured me that I will receive my loan from them. On a second thought, due to my homelessness I had to take a trial and applied for the loan, luckily for me I received a loan of $80,000.00 from Mr, Benjamin. I'm happy I took the risk and applied for the loan. My kids have been given back to me and now I own a home and a business of my own. All thanks and gratitude goes to Le_Meridian Funding Service and for the help of Mr, Benjamin for giving me a meaning to life when i had lost all hope. If you currently seeking for a loan assistance, you can contact them via: { lfdsloans@outlook.com / lfdsloans@lemeridianfds.com} Or WhatsApp +1-989-394-3740
Post a Comment